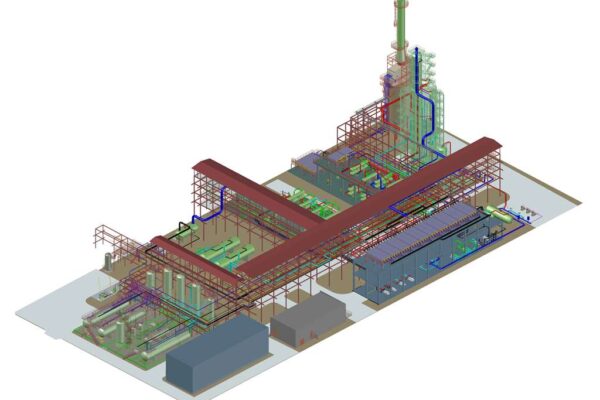
ООО «НЕФТЕГАЗ-ИНЖИНИРИНГ», 2023
ООО "НЕФТЕГАЗ-ИНЖИНИРИНГ"
Согласно технологическому регламенту на проектирование ЦПС на месторождении им. Р. Требса и им. А. Титова электродегидраторы размещены в две нитки, а для возможности применения одноступенчатого обессоливания и глубокого обезвоживания нефти электродегидраторы могут работать как параллельно, так и последовательно. При выводе одного из электродегидраторов ЭДГ-1 – ЭДГ-3 на ремонт, обвязка предусматривает работу оставшихся двух электродегидраторов параллельно, тем самым обеспечивая совместную подготовку нефтей месторождений имени Р. Требся и имени А. Титова. Данный проект разработан для первого этапа строительства, строительство электродегидратора ЭДГ-3 предусмотрено во втором этапе.
Ввиду географического положения объекта строительства в районе крайнего севера, основным требованием было предусмотреть в проекте конструктивные решения, позволяющие изготовить блок полностью в заводских условиях с последующей транспортировкой на месторождение. Проект предусматривает сборку и испытания на заводе-изготовителе, последующую разборку на транспортировочные узлы и монтаж на месторождении. Конструктивные решения, предусмотренные в проекте, сводят к минимуму сварочные работы при сборке блока.
Система автоматизации блока обеспечивает полноценную и эффективную работу без постоянного присутствия обслуживающего персонала и имеет возможность автоматического регулирования и дистанционного управления.
Мобильная блочная сепарационно-наливная установка (МБСНУ) предназначена для очистки попутного нефтяного и природного газов от капельной жидкости и механических примесей, измерения расходов нефти и газа, вывоза нефти автоцистернами, подачи отсепарированного природного и попутного нефтяного газа в трубопроводную систему транспорта, выработки электроэнергии на газопоршневой электростанции для обеспечения МБСНУ электроэнергией.
Установка состоит из 12 основных блоков, которые включают в себя более 15 единиц технологического оборудования: блок нефтегазового сепаратора первой ступени и газового сепаратора; блок нефтегазового сепаратора второй ступени и фильтра очистки газа; блок накопительной емкости; блок факельных сепараторов; блок факельной установки; блок автоматизированного стояка налива нефти; блок дренажной емкости; блоки арматурных площадок; блок газопоршневой электростанции; блок трансформаторной подстанции; блок операторной.
Установка собирается из блоков полной заводской готовности (с оборудованием, всеми необходимыми трубопроводами, запорно-регулирующей арматурой, предохранительными клапанами, приборами КИПиА, электротехническим оборудованием и кабельной продукцией). Блоки устанавливаются на заранее подготовленный фундамент из дорожных плит, уложенных на песчано-гравийное основание. Межблочные технологические трубопроводы, электрические линии и линии КИПиА имеют легкосборные мобильные эстакады для их прокладки.
Нормальный режим работы установки предусматривает отсутствие внешнего источника электроэнергии. Для обеспечения потребности в электроэнергии и тепле предусмотрен блок газопоршневой электростанции, работающей на газе после сепаратора второй ступени. В качестве резервного источника питания в составе установки предусмотрен блок трансформаторной подстанции, который в случае отключения газопоршневой электростанции обеспечивает установку электроэнергией от ближайшей высоковольтной сети. В составе установки предусмотрен блок операторной с автоматизированными рабочими местами, с которых осуществляется контроль и управление технологическими процессами.
Установка предназначена для применения в зоне степного климата, характерной чертой которого является резкая континентальность: жаркое и сухое лето с частыми засухами (+42°C) и холодная малоснежная зима (‐37°C) с частыми оттепелями.
Установка предназначена для слива сжиженного пропана из танк‐контейнеров. Предусматривается одновременный слив сжиженного пропана из двух танк‐контейнеров. Система слива пропана размещается на открытой площадке. Производительность установки – 45 м3/ч, общее количество отгружаемого продукта – 867 тонн (с учетом однократной засыпки сорбента). Осушка пропана до требуемых технологических параметров (вода – 10 ppm об., CO2 ‐ 200 ppm об., Сера ‐ 30 ppm масс., H2S ‐ 5 ppm масс., ртуть – 10 нанограмм м/ст. м3) осуществляется в осушителе посредством применения молекулярных сит фирмы AXENS.
Передвижная установка слива пропана представляет собой собранный блок на передвижной раме с оборудованием, всеми необходимыми трубопроводами, запорно-регулирующей арматурой, предохранительными клапанами, приборами КИПиА, электротехническим оборудованием и кабельной продукцией. Насосный агрегат установки подобран из условия заданных параметров по производительности и напора. Примечательной чертой используемого насоса является низкий кавитационный запас (0,5 м), наличие системы торцевых уплотнений по типу API Plan 52. Для периодического перемещения установки ее конструкция предусмотрена компактной и мобильной и исключает дополнительную сборку на месте монтажа. Подключение установки к производственным сетям и танк‐контейнерам осуществляется посредством гибких соединений из нержавеющей стали и специально изготовленных присоединительных устройств. Установка предназначена для применения в условиях Крайнего севера (‐56°C). Проект установки разработан на двух языках – русском и английском.
Узлы чешуирования, брикетирования и аспирации, в составе первого в России и странах СНГ производства малеинового ангидрида, предназначены для получения твердых товарных брикетов из жидкого расплава МАН, с дальнейшей упаковкой в HDPE-мешки по 25 кг на паллеты.
Расплавленный малеиновый ангидрид от питающих насосов подается на узел чешуирования для получения чешуек посредством кристаллизации жидкого МАН на поверхности барабана кристаллизатора. Для равномерного охлаждения барабана в его внутреннюю полость, через форсунки, обеспечивается циркуляция захоложенной воды от установки охлаждения, входящей в состав узла чешуирования. Затвердевший слой постоянно срезается специальным ножом, рассыпаясь при этом на чешуйки. Чешуйки под действием силы тяжести поступают на дробилки узла брикетирования. Помол от дробилок посредством ковшового элеватора направляется в питающий бункер, а затем на шнековые питатели валкового пресса. Произведенные на прессе брикеты МАН направляются для сортировки на грохот, где отсеянная некондиция возвращается в ковшовый элеватор, а товарные брикеты выводятся на ленточный конвейер, откуда попадают в блок упаковки и паллетирования.
Узлы состоят из следующего основного технологического оборудования: кристаллизаторы; чиллер хладагента с насосами; буферная емкость хладагента; дробилки; питающий бункер; ковшовый элеватор; валковый пресс; грохот для брикетов; ленточный конвейер; осушители воздуха с чиллером охлаждения и насосами; рукавные фильтры и циклоны; воздуходувки; электрический нагреватель воздуха.
Малеиновый ангидрид — токсичное высокоопасное вещество с резким запахом, вследствие чего в рабочей зоне должны соблюдаться жесткие требования по предельно допустимой концентрации продукта (не более 10 мг/м3). Мало того, твердый малеиновый ангидрид очень гигроскопичен, из-за чего имеются ограничения по содержанию влаги в окружающем продукт воздухе. Для комплексного решения данной проблемы предусмотрен узел аспирации с подачей осушенного воздуха к оборудованию узлов чешуирования, брикетирования и упаковки, и удалением паров и пыли малеинового ангидрида. Уловленная в фильтрах аспирации пыль посредством циклонов возвращается к питающему бункеру брикетирования для последующей переработки в брикеты, а обеспыленный воздух удаляется из системы вакуумными воздуходувками и выводится за пределы здания на мокрую очистку в скруббер. Таким образом, за счет использования передовой технологии и уникального оборудования, исключается негативное воздействие на окружающую среду.
Узлы чешуирования, брикетирования и аспирации располагаются на многоуровневой этажерке, в отдельном помещении с габаритами в плане 36 х 24 метров, и высотой 29 метров. Большая высота этажерки обусловлена тем, что практически весь технологический процесс протекает под действием силы тяжести. Компоновка оборудования и грузоподъемные механизмы подобраны исходя из максимального удобства обслуживания и ремонта.
Всё основное оборудование, примененное в проекте, изготовлено в Италии, Германии и Франции. Одной из главных задач и особенностей данного проекта является интеграция всего оборудования в единую автоматизированную безопасную систему, соответствующую российским нормам.
Установка предназначена для очистки, осушки, замера, редуцирования газа с целью использования его в качестве топливного газа для трёх ГПА Solar Turbines, буферного газа для системы сухих газодинамических уплотнений нагнетателей ГПА, импульсного газа для управления пневмоприводной арматурой на площадке КС, топливного газа для собственных нужд УКПГ Марковского НГКМ, для котельной УКПГ и ОБП, топливного газа для газотурбинной электростанции. Основным источником входящего газа является сухой отбензиненный газ после первой ступени компримирования (вход 1) и газ от входного коллектора КС (вход 2). Режим работы – постоянный.
Установка представляет собой одноэтажное здание размером 5,2х21м, категории А по взрывопожарной и пожарной опасности, состоящее из утепленных транспортных модулей полной заводской готовности и смонтированного в них технологического оборудования, запорной и регулирующей арматуры, трубопроводов, систем электроснабжения, КИП и А, отопления, вентиляции, охранно-пожарной сигнализации, пожаротушения, связи и т.д. Модули устанавливаются на заранее подготовленный фундамент, тем самым собираются в готовое здание. Здание состоит из 4х помещений (помещение подготовки газа, электрощитовая, котельная и подсобное помещение), в которых размещается около 10 единиц технологического оборудования: фильтры-сепараторы, теплообменники нагрева газа, фильтры газа, электронагреватель, адсорберы-осушители с возможностью регенерации, котел нагрева теплоносителя, насосное и вспомогательное оборудование. Установка полностью автоматизирована и оснащена локальной системой управления с возможностью подключения к основной системе управления УКПГ. Установка разработана с учетом возможности эксплуатации и хранения в районах с холодным и умеренным климатом УХЛ1 по ГОСТ 15150-69.
Блок реактора получения бензина совместной переработки углеводородного сырья и метанола предназначен для конвертирования лёгкого углеводородного сырья и метанола в основу высокооктанового бензина с низким содержанием бензола и повышенным содержанием ксилолов. Блок реактора располагается на открытой площадке. Производительность установки – 1,5 т/ч по сырьевой смеси. Процесс получения в реакторе газожидкостной смеси осуществляется за счет прохождения потоков через четыре реакционные зоны с неравномерным неподвижным объёмом катализатора и зоны нагрева газового потока. Катализатор расположен на полках, которые образуют реакционные зоны. Перед реакционными зонами имеются зоны смешения и выравнивания потоков.
Блок реактора получения бензина совместной переработки углеводородного сырья и метанола выполнен в блочно-модульном исполнении в комплекте с трубопроводной обвязкой, приборами КИПиА, освещением, площадками обслуживания, лестницами и т.д., что значительно упрощает процесс сборки и пуска объекта в эксплуатацию.
Главной особенностью данного блока являются очень высокие температуры, при которых протекает процесс синтеза газа и регенерации катализатора. При этом малейшее изменение температуры в реакционной зоне влияет на качество процесса. В связи с этим температура в слое катализатора измеряется в 8 точках каждой полки реактора, а поддержание температуры и дополнительный нагрев потоков осуществляется за счет трех мощных электрических ТЭНов, расположенных перед каждой реакционной зоной. Конструкция реактора обеспечивает возможность регенерации катализатора, состоящей из продувки азотом и продувки воздухом с постепенным увеличением температуры. Большое внимание при разработке данного проекта было уделено теплоизоляции, необходимой для обеспечения тепловых потерь, не превышающих уровень, при котором нарушатся условия проведения процесса, а также для соблюдения санитарных норм и норм по охране труда.
Блоки сепараторов С-101/4,5 и С-102/4,5 входят в состав оборудования установки низкотемпературной сепарации УКПГ, предназначены для разделения предварительной очистки сырого природного газа от механических примесей, газового конденсата и пластовой воды перед последующей его переработкой. За счет простой, но эффективной конструкции, обеспечивается высокая производительность, а высокая степень сепарации гарантируется за счет применения специальных коалесцирующих насадок вне зависимости от давления. Дополнительный элементом является отдельная секция вертикального центробежного сепаратора, основанная на вихревом эффекте, где под силой тяжести вся выделившаяся жидкость скапливается в нижней части и отводится в горизонтальный сепаратор, а очищенный газ, наоборот, поднимается вверх и выходит за границы блока. Блок выполнен в виде узла полной заводской готовности, с трубопроводами и КИПиА, на единой раме, разбираемой на несколько транспортировочных частей. Данное исполнение позволило значительно оптимизировать стоимость транспортировки, а также ускорить процесс сборки и пуска объекта в эксплуатацию.
В состав блока сепаратора входят: сепаратор горизонтальный, сепаратор газожидкостной вертикальный вихревого типа, несущая рама, трубопроводная обвязка и ЗРА, площадки обслуживания, КИПиА и кабельная продукция.
Установка ЭЛОУ-АТ-7 находится на территории действующего Туркменбашинского Комплекса Нефтеперерабатывающих Заводов и предназначена для электрообессоливания, обезвоживания и атмосферной перегонки нефти.
Расчетная производительность установки по перерабатываемой нефти составляет 3,0 млн. т/год. Основными продуктами переработки нефти, получаемыми на установке ЭЛОУ АТ-7, являются легкий бензин, тяжелый бензин, неочищенный компонент керосина авиационного ТС-1 (либо осветительный керосин КО-20 как компонент товарных керосинов), дизельное топливо (компонент сырья установки гидроочистки или товарного дизельного топлива), мазут. Установка состоит из 13 блоков, которые включают в себя более 130 единиц технологического оборудования: блок теплообменников до ЭЛОУ; блок теплообменников после ЭЛОУ; блок ЭЛОУ; печной блок; блок колонн; блок конденсации, охлаждения и подачи продуктов; блок рефлюксной емкости и емкостей реагентов с дозировочными насосами; блок щелочной очистки; блок заглубленных емкостей; блок пенообразователя; центральный пункт управления (ЦПУ); эстакады и ресивер воздуха КИП; трансформаторная подстанция; блок факельного сепаратора.
К строительным особенностям объекта прежде всего относится расположение Туркменбашинского Комплекса Нефтеперерабатывающих Заводов. Запроектированные здания и сооружения располагаются в районе с сейсмичностью 9 баллов, в связи с чем были соблюдены требования к расчету с учетом сейсмических нагрузок, обеспечивающие сейсмостойкость конструкций.
На установке ЭЛОУ-АТ-7 был запроектирован центральный пункт управления, который является общей операторной для установок ЭЛОУ-АТ 2, 6 и 7. Их суммарная мощность по перерабатываемому сырью составляет 7,5 млн. т/год. Также запроектирован единый для установок ЭЛОУ-АТ-6 и ЭЛОУ-АТ-7 блок щелочной очистки дизельного топлива и керосинов. Строительство этого блока продиктовано рачительным использованием промышленной территории и требованиями по защите окружающей среды.
В рамках реализации данного проекта также было предусмотрено расширение существующего распределительного пункта 6кВ и проектирование нового ремонтно-механического цеха.